Spis treści
Co to jest Lean?
Podejście Lean w zarządzaniu, znane również jako Lean manufacturing, koncentruje się na eliminowaniu marnotrawstwa, jednocześnie maksymalizując wartość, jaką oferujemy naszym klientom. Filozofia ta skupia się na dostrzeganiu i usuwaniu działań, które nie przynoszą korzyści z perspektywy odbiorcy.
Współpraca między menedżerami a pracownikami odgrywa kluczową rolę, tworząc atmosferę zaangażowania i ciągłego doskonalenia procesów. Lean wywodzi się z systemu produkcji Toyoty (TPS) i wykorzystuje szereg technik mających na celu optymalizację działań. Warto podkreślić, że podejście to nie ogranicza się jedynie do poprawy wydajności, ale również promuje zrównoważony rozwój oraz innowacje.
Takie elementy mają istotny wpływ na długoterminową wartość dostarczaną klientom oraz na efektywność operacyjną firm. Ponadto, skuteczne wdrażanie Lean wymaga aktywnego zaangażowania pracowników i ciągłego monitorowania procesów, co pozwala na wychwycenie obszarów wymagających poprawy.
Jakie są podstawowe zasady metodyki Lean?
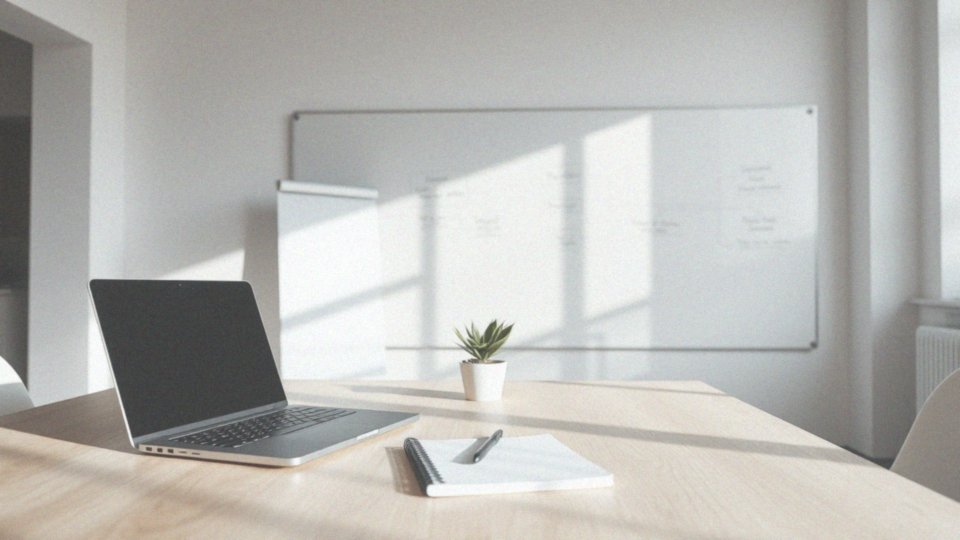
Podstawowe zasady metodyki Lean obejmują istotne aspekty, które pomagają w maksymalizacji wartości dla klientów. Na początek warto zidentyfikować, co w oczach odbiorców jest naprawdę istotne. Dzięki temu zyskujemy lepsze zrozumienie tego, co powinniśmy uwzględnić w naszych ofertach.
Następnym krokiem jest analiza strumienia wartości, czyli mapowanie działań, które pozwala na wykrycie marnotrawstwa. Kluczowym elementem Lean jest także wprowadzenie płynnego przepływu materiałów, co wspiera zasady Pull oraz produkcję Just In Time, a w rezultacie pomaga w redukcji zapasów i zwiększa efektywność operacyjną.
Ciągłe doskonalenie to kolejny fundamentalny aspekt tej filozofii. To oznacza, że zawsze poszukujemy innowacyjnych sposobów na usprawnienie procesów. Skoncentrowanie się na płynności i dążenie do doskonałości sprzyjają tworzeniu kultury nieustannego udoskonalania w organizacji.
Taka atmosfera nie tylko zwiększa wydajność, ale również angażuje pracowników, którzy czują się odpowiedzialni za jakość realizowanych procesów. Te wszystkie elementy współdziałają, mając na celu dostarczenie większej wartości klientom oraz poprawę rentowności organizacji.
Co oznacza eliminacja strat w koncepcji Lean?
Eliminacja strat w ramach koncepcji Lean polega na identyfikowaniu i eliminowaniu wszelkich działań, które nie przyczyniają się do wartości dodanej dla klientów. Kluczowe straty, zwane Muda, obejmują m.in.:
- nadprodukcję, co prowadzi do gromadzenia dużych zapasów,
- czas oczekiwania, który spowalnia procesy,
- transport i nadmierne przetwarzanie, które generują niepotrzebne koszty,
- ruch pracowników oraz ich niewłaściwe wykorzystanie, co znacząco obniża efektywność operacyjną.
Skuteczna eliminacja strat wiąże się z wieloma korzyściami. Przede wszystkim pozwala na:
- obniżenie kosztów operacyjnych,
- skrócenie czasu realizacji zamówień,
- usprawnienie jakości produktów.
Wdrożenie podejścia Just In Time umożliwia elastyczne dostosowanie produkcji do rzeczywistych potrzeb rynku, co daje organizacjom przewagę konkurencyjną dzięki lepszemu zagospodarowaniu zasobów. Te działania pozytywnie wpływają na satysfakcję i lojalność klientów. Podejście Lean skupia się na ciągłym doskonaleniu procesów, co nie tylko sprzyja innowacjom, ale także kształtuje kulturę zaangażowania całego zespołu w dążenie do minimalizacji marnotrawstwa.
Co to są straty typu Muda i jak wpływają na Lean?
Straty typu Muda to wszelkie działania lub procesy, które nie przynoszą wartości klientowi, a jednocześnie pochłaniają cenne zasoby. Można je sklasyfikować w siedmiu istotnych kategoriach:
- nadprodukcja,
- czas oczekiwania,
- transport,
- nadmierne przetwarzanie,
- zapasy,
- przemieszczanie się oraz
- wady.
Każda z tych grup przyczynia się do wzrostu kosztów, obniżenia jakości oraz wydłużenia czasu produkcji. Eliminacja strat Muda jest kluczowym elementem podejścia Lean i ma istotny wpływ na efektywność oraz optymalizację procesów. Na przykład, nadprodukcja prowadzi do gromadzenia zbędnych zapasów, co skutkuje wyższymi kosztami przechowywania i ryzykiem przestarzałych produktów. Czas oczekiwania spowalnia całe procesy, co negatywnie wpływa na wydajność. Aby transport był efektywny, konieczne jest staranne planowanie. Zbyt duża ilość przetwarzania często wynika z nieprawidłowego zarządzania zasobami, co prowadzi do marnotrawstwa. Przemieszczanie się pracowników w niewłaściwy sposób wprowadza chaos i marnuje cenny czas. Dodatkowo, wady w produktach generują koszty związane z reklamacjami oraz koniecznością ponownej produkcji. Redukcja strat Muda daje organizacjom szansę na znaczną poprawę jakości oferowanych produktów i usług. Przyczynia się to do budowania długotrwałych relacji z klientami oraz tworzenia bardziej elastycznych i odpornych procesów produkcyjnych. Co więcej, eliminowanie tych strat prowadzi do obniżenia kosztów operacyjnych, co jest niezbędne dla osiągania zysku w konkurencyjnym środowisku rynkowym.
Jak Lean minimalizuje marnotrawstwo?
Lean skutecznie zmniejsza straty poprzez różne działania. Skupia się na identyfikacji oraz eliminacji marnotrawstwa, które w terminologii Lean określane jest jako Muda, w operacjach biznesowych. Kluczowe metody, takie jak analiza strumienia wartości, umożliwiają zrozumienie, jak przepływają materiały i informacje w procesach. Taki wgląd pozwala zidentyfikować czynności, które nie dodają wartości z perspektywy klienta.
Na przykład, techniki takie jak:
- 5S,
- Poka-Yoke,
- Kanban przyczyniają się do stworzenia bardziej uporządkowanego oraz efektywnego środowiska pracy.
Metoda 5S ułatwia utrzymanie porządku na stanowiskach, co znacząco redukuje czas potrzebny na odnalezienie narzędzi i minimalizuje ryzyko pomyłek. W ramach Lean, standaryzacja procesów zwiększa efektywności przez eliminację zbędnych kroków i stabilizację wyników. Wizualizacja działań dodatkowo poprawia zrozumienie poszczególnych procesów, co umożliwia szybkie wykrywanie potencjalnych problemów.
Ograniczenie marnotrawstwa prowadzi również do:
- obniżenia kosztów operacyjnych,
- skrócenia czasu realizacji zamówień.
Efektem tych usprawnień jest polepszenie jakości produktów, co pozwala organizacjom lepiej odpowiadać na potrzeby klientów i zwiększać ich satysfakcję. Lean, dzięki swojemu zintegrowanemu podejściu, sprzyja długoterminowemu sukcesowi firm oraz promuje kulturę nieustannego doskonalenia i innowacji.
Jakie narzędzia wspierają optymalizację procesów w Lean?
W metodologii Lean istnieje wiele przydatnych narzędzi, które mają na celu optymalizację procesów. Ich głównym zamysłem jest redukcja strat i poprawa efektywności. Do najważniejszych narzędzi należą:
- analiza strumienia wartości (VSM) – pozwala na wizualizację oraz ocenę przepływu materiałów i informacji,
- metoda 5S – składająca się z pięciu etapów: Selekcja, Systematyka, Sprzątanie, Standaryzacja oraz Samodyscyplina, sprzyja organizacji stanowiska pracy,
- Poka-Yoke – skoncentrowana na zapobieganiu błędom, wprowadza mechanizmy zabezpieczające, które redukują ryzyko pomyłek,
- Kanban – system sterowania procesami produkcyjnymi, umożliwiający efektywne zarządzanie zapasami oraz dostosowywanie produkcji do potrzeb rynku,
- wizualna kontrola przepływu materiałów – pozwala na szybką identyfikację wąskich gardeł,
- standaryzacja pracy – wzmocniona cyklem PDCA (Plan-Do-Check-Act), wspiera ciągłe doskonalenie,
- analiza wartości – skupia się na eliminacji zbędnych działań, co prowadzi do maksymalizacji wartości dodanej dla klienta.
Wszystkie te narzędzia są nieocenione w realizacji celów Lean, takich jak zwiększenie wydajności i redukcja strat.
Jakie są kluczowe metody w Lean, takie jak 5S i Kaizen?
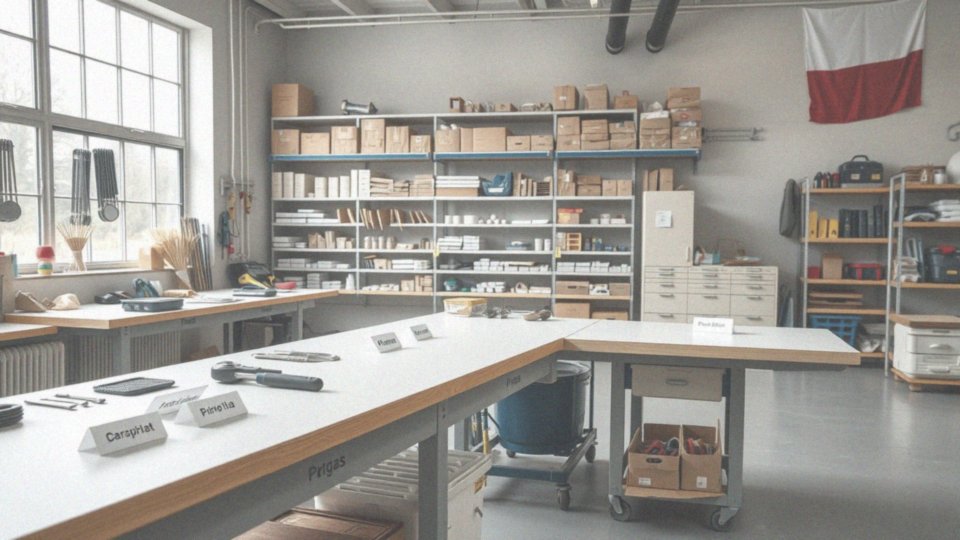
W ramach podejścia Lean wyróżniamy dwa kluczowe narzędzia: 5S i Kaizen, które odgrywają fundamentalną rolę w zwiększaniu efektywności firm oraz eliminowaniu marnotrawstwa.
Metoda 5S obejmuje pięć etapów:
- Selekcję,
- Systematyzację,
- Sprzątanie,
- Standaryzację,
- Samodyscyplinę.
Jej głównym celem jest stworzenie zorganizowanego i efektywnego środowiska pracy, co znacznie minimalizuje czas poświęcony na szukanie potrzebnych narzędzi. Dodatkowo, poprawa porządku wpływa pozytywnie na bezpieczeństwo, co z kolei przekłada się na wydajność całych procesów.
Kaizen, z kolei, to filozofia nieustannego doskonalenia. Angażuje wszystkich pracowników, promując wprowadzanie systematycznych, małych zmian. Taki sposób działania pozwala firmom na osiąganie znacznych oszczędności oraz podnoszenie jakości oferowanych produktów i usług.
Co więcej, Kaizen kształtuje kulturę zaangażowania, w której pracownicy czują się odpowiedzialni za realizowane zmiany. Oba te podejścia sprzyjają zwiększeniu efektywności oraz zadowolenia klientów. Dzięki nim firmy mogą skutecznie redukować odpady oraz wdrażają innowacyjne rozwiązania, co prowadzi do długotrwałego sukcesu na rynku.
W jaki sposób ciągłe doskonalenie wpływa na Lean?
Ciągłe doskonalenie, znane jako Kaizen, odgrywa istotną rolę w filozofii Lean, wpływając na różnorodne aspekty funkcjonowania organizacji. Działania związane z tą metodą koncentrują się na:
- nieustannym udoskonalaniu istniejących procesów,
- eliminacji marnotrawstwa,
- zwiększaniu efektywności,
- poprawie jakości oferowanych produktów i usług.
Zaangażowanie całego zespołu w proces doskonalenia sprzyja budowaniu kultury odpowiedzialności, w której pracownicy aktywnie uczestniczą w wprowadzaniu zmian. Ciągłe uczenie się to kluczowy element Kaizen, umożliwiający organizacjom identyfikację potencjalnych obszarów do poprawy na podstawie doświadczeń z przeszłości. Regularne spotkania i sesje feedbackowe sprzyjają wymianie spostrzeżeń oraz pomysłów na usprawnienia, co przyczynia się do jeszcze lepszej optymalizacji procesów. Dążyć do innowacji oznacza wprowadzać zmiany, które odpowiadają dynamicznym potrzebom rynku, co ma bezpośredni wpływ na rozwój zaawansowanych produktów oraz jakość obsługi klienta.
W rezultacie rozwój kultury zaangażowania oraz współpracy zespołowej wspiera efektywność operacyjną, co przekłada się na wyższą satysfakcję klientów. Ciągłe doskonalenie stanowi zatem kluczowy komponent zasad Lean, a jego skuteczne wdrażanie sprzyja długotrwałemu rozwojowi organizacji oraz ich adaptacji w zmieniającym się otoczeniu rynkowym.
Jak Lean poprawia wydajność procesów produkcyjnych?
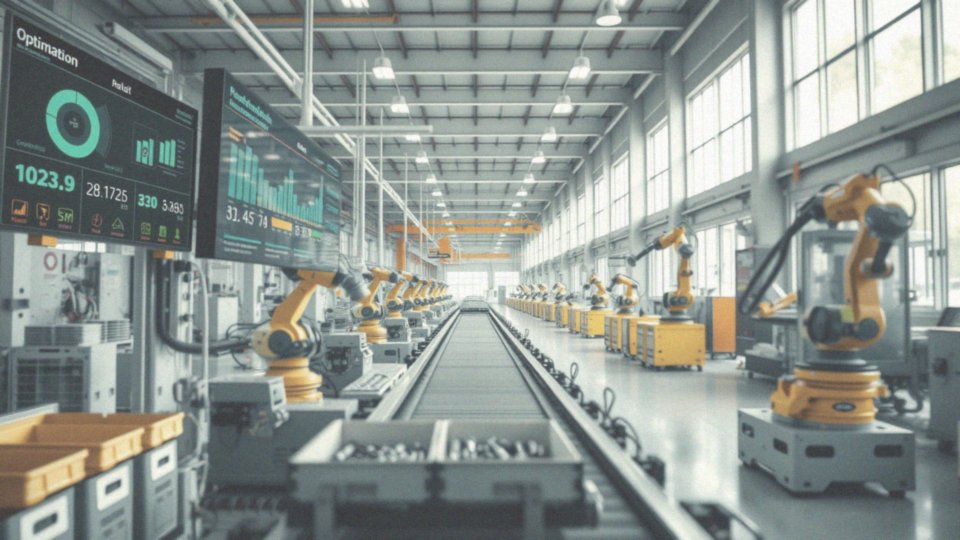
Lean znacząco podnosi efektywność procesów produkcyjnych poprzez usuwanie marnotrawstwa oraz doskonalenie łańcucha wartości. Kluczowym elementem tej metody jest skrócenie czasu cyklu, co sprzyja szybszym realizacjom zamówień i lepszemu dostosowaniu produkcji do zmieniających się potrzeb rynku.
Dzięki zastosowaniu zasady Just In Time organizacje są w stanie:
- zredukować zapasy,
- obniżyć koszty związane z magazynowaniem,
- minimalizować ryzyko posiadania przestarzałych towarów.
Standaryzacja procesów oraz ich wizualizacja przyczyniają się do zwiększenia efektywności operacyjnej. Wyraźne standardy sprawiają, że pracownicy lepiej rozumieją swoje zadania, co nie tylko redukuje ilość błędów, ale także podnosi jakość oferowanych produktów.
Zaangażowanie pracowników w procesy ulepszania zwiększa ich motywację, co bezpośrednio przekłada się na wyższą wydajność oraz lepsze rezultaty w zakresie jakości wyrobów. Dzięki tym wszystkim działaniom firmy mogą:
- realizować zamówienia w krótszym czasie,
- obniżać koszty operacyjne,
- poprawić swoje wyniki finansowe.
Lean to nie tylko narzędzie do wzmacniania efektywności, ale także podejście, które sprzyja tworzeniu elastycznych i odpornych systemów produkcyjnych. To z kolei zwiększa konkurencyjność przedsiębiorstw na dynamicznie zmieniającym się rynku.
Jak wdrażanie Lean wpływa na wartości dla klientów?
Wdrożenie metodologii Lean ma istotne znaczenie dla wartości, jaką otrzymują klienci. Głównym celem jest maksymalizacja korzyści, co prowadzi do poprawy jakości produktów. Dzięki temu wzrasta satysfakcja odbiorców.
Eliminując wszelkie marnotrawstwa, proces wydajnościowy przyspiesza czas realizacji zamówień, umożliwiając jednocześnie szybsze reagowanie na potrzeby rynku. Co więcej, Lean przyczynia się do obniżenia kosztów, co pozwala firmom oferować atrakcyjne ceny.
Elastyczność w dostosowywaniu się do wymagań klientów staje się kluczowym atutem. Organizacje, które implementują zasady Lean, lepiej adaptują się do zmieniających się preferencji rynkowych, co zwiększa ich przewagę konkurencyjną.
Klient w centrum uwagi to fundamentalny aspekt strategii Lean. Dążenie do zapewnienia wartości, która odpowiada na indywidualne potrzeby konsumentów, wzmacnia ich lojalność. Takie podejście sprzyja również budowaniu trwałych relacji, korzystnych zarówno dla firm, jak i ich klientów.
W konsekwencji, zastosowanie Lean ma znaczący wpływ na konkurencyjność i efektywność operacyjną, co bezpośrednio przekłada się na wartość oferowaną klientom. Skupienie na jakości, zamiast jedynie na cięciach kosztów, staje się kluczowym elementem sukcesu w szybko zmieniającym się świecie biznesu.
Jak Lean wspiera rozwój kultury zaangażowania w firmie?
Lean kształtuje kulturę zaangażowania w przedsiębiorstwach poprzez zestaw kluczowych praktyk, z naciskiem na:
- zespołową współpracę,
- efektywną wymianę pomysłów,
- harmonijne działanie razem.
Regularna komunikacja sprzyja otwartości i przejrzystości, co w rezultacie przyspiesza rozwiązywanie problemów i zauważanie obszarów do doskonalenia. Ciągłe uczenie się to kolejny istotny element wpływający na zaangażowanie. Warsztaty, szkolenia oraz sesje feedbackowe są integralną częścią dnia pracy, co przyczynia się do rozwijania umiejętności oraz wiedzy zespołu. Pracownicy mają okazję delegować odpowiedzialności, co wzmaga ich poczucie wpływu na przebieg procesów oraz osiągane wyniki.
Praktyki Lean, takie jak Kaizen bądź metoda 5S, stają się fundamentem kultury organizacyjnej. W takich środowiskach każdy członek zespołu odczuwa osobistą odpowiedzialność za jakość oraz efektywność swoich działań. Dodatkowo, wprowadzenie systemów nagradzania za innowacyjne propozycje i ich wdrażanie stymuluje pracowników do aktywnego uczestnictwa w procesach ciągłego doskonalenia. W efekcie tych działań można zaobserwować pozytywne rezultaty, co tylko zwiększa zaangażowanie oraz lojalność wobec organizacji.
W jaki sposób Lean stawia na współpracę między pracownikami a menedżerami?
Lean opiera się na bliskiej współpracy między pracownikami a menedżerami, co jest zasadniczym elementem skutecznego wprowadzania tej filozofii. Kluczowa jest otwarta komunikacja, która pozwala wszystkim lepiej rozumieć potrzeby oraz oczekiwania drugiej strony. Razem identyfikują problemy i wdrażają efektywne rozwiązania, co obfituje korzyściami dla całego zespołu.
W kulturze zaangażowania pracownicy czują się zmotywowani do aktywnego uczestniczenia w procesie doskonalenia, co zwiększa ich poczucie odpowiedzialności. Rola menedżerów jako mentorów i liderów jest nieoceniona, ponieważ zapewniają oni wsparcie w rozwijaniu umiejętności oraz eliminacji marnotrawstwa.
Dzięki delegowaniu odpowiedzialności można budować zaufanie w zespole, umożliwiając pracownikom podejmowanie decyzji w swoich obszarach. Taka autonomia sprzyja innowacjom oraz lepszemu wykorzystaniu dostępnej wiedzy.
Przykładem efektywnej pracy zespołowej są:
- cykliczne spotkania,
- wymiana informacji na temat postępów w projektach.
To podejście pozwala zespołowi na lepsze dostosowanie się do dynamicznie zmieniającego się otoczenia rynkowego, co zwiększa elastyczność i konkurencyjność organizacji. Kultura ciągłego doskonalenia staje się integralną częścią codzienności, sprzyjając atmosferze współpracy i innowacyjności.
Taka wspólna praca wpływa na poprawę efektywności operacyjnej oraz przekłada się na lepsze wyniki i większą satysfakcję zarówno pracowników, jak i klientów.
Jakie są wyzwania w implementacji Lean w organizacji?
Wdrażanie metodyki Lean w organizacji niesie ze sobą szereg wyzwań, które mogą znacznie utrudnić skuteczną realizację oraz osiąganie zamierzonych efektów. Oto kluczowe trudności, z którymi można się spotkać:
- Opór przed zmianami: Wiele osób w firmach obawia się nowości, co może prowadzić do opóźnień i frustracji w zespole, obawy często dotyczą utraty komfortu, jaki zapewnia dotychczasowy sposób pracy.
- Niedostateczne wsparcie kierownictwa: Skuteczne wdrożenie Lean wymaga mocnego zaangażowania menedżerów, brak aktywnego uczestnictwa ze strony liderów może negatywnie wpłynąć na morale pracowników oraz ich zaufanie do inicjatyw związanych z Lean.
- Ograniczone zasoby: Niedobór zasobów, zarówno ludzkich, jak i finansowych, stanowi dużą przeszkodę w efektywnym wprowadzaniu zmian, niejednokrotnie organizacje zmagają się z problemem alokacji czasu i funduszy na szkolenia oraz wprowadzenie nowych narzędzi.
- Brak wiedzy i umiejętności: Niska znajomość zasad Lean znacząco wpływa na skuteczność procesu, choć szkolenia są niezbędne, to jeśli pracownicy nie są odpowiednio przygotowani, wprowadzenie Lean może stać się trudne.
- Niewłaściwe zrozumienie filozofii Lean: Lean to nie tylko zestaw narzędzi, ale także zmiana kultury organizacyjnej, pracownicy, którzy nie widzą celów i korzyści płynących z tej metody, mogą nie być skłonni do aktywnej współpracy.
- Brak kultury ciągłego doskonalenia: Implementacja Lean opiera się na dążeniu do permanentnego ulepszania procesów, w firmach, które nie wdrażają takiego podejścia, osiągnięcie oczekiwanych rezultatów bywa trudne.
- Trudności z pomiarem wyników: Opracowanie klarownych wskaźników sukcesu Lean może być wyzwaniem, brak wymiernych rezultatów osłabia wiarę w proces transformacji, co prowadzi do frustracji w zespole.
Aby skutecznie pokonać te przeszkody, ważne jest silne przywództwo, systematyczne szkolenia, otwarta komunikacja oraz zaangażowanie wszystkich pracowników. Tylko wtedy organizacja zdoła w pełni wykorzystać potencjał metodyki Lean, co przyczyni się do optymalizacji procesów oraz poprawy efektywności operacyjnej.
Jakie korzyści płyną z wdrożenia filozofii Lean?
Wdrożenie filozofii Lean oferuje liczne korzyści dla organizacji. Przede wszystkim przyczynia się do obniżenia kosztów operacyjnych, co przekłada się na znaczne oszczędności. Eliminacja działań, które nie wnoszą wartości dodanej, skutkuje:
- bardziej efektywnym wykorzystaniem dostępnych zasobów,
- zwiększeniem wydajności procesów,
- przyspieszeniem realizacji zadań,
- skróceniem czasu dostaw.
Dodatkowo, poprawa jakości oferowanych produktów i usług podnosi poziom satysfakcji klientów. Klienci, otrzymując lepsze wyroby, stają się bardziej lojalni i ufają marce. Kultura Lean zachęca również pracowników do aktywnego uczestnictwa w optymalizacji procesów. W rezultacie czują oni większą odpowiedzialność za osiągane wyniki, co wpływa na ich zaangażowanie. Dzięki eliminacji nieefektywnych działań, zwiększa się także bezpieczeństwo w miejscu pracy, co redukuje ryzyko wypadków.
Organizacje, które wdrażają zasady Lean, zyskują przewagę na rynku dzięki większej elastyczności oraz szybkości adaptacji do zmieniających się potrzeb. Umiejętność błyskawicznego reagowania na oczekiwania klientów staje się kluczowym atutem, przyczyniając się do długofalowego sukcesu i stabilności na różnorodnych rynkach. Lean wspiera również proces innowacji oraz pomaga w budowaniu zdrowej, dynamicznej kultury organizacyjnej.